材料の入数を揃える…バラバラの時の発注、入庫、仕掛、在庫管理の工数を考えましょう
改善
2022.01.03
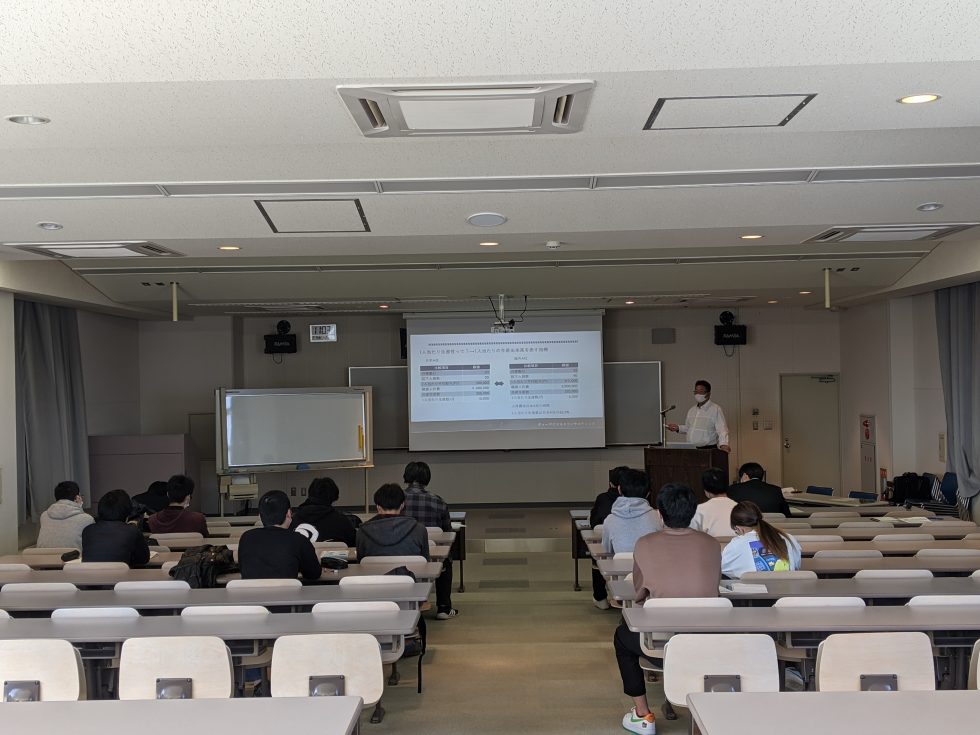
地域活性化の為に魅力ある地方企業づくりのお手伝いをさせて頂く、
ディーズビジネスコンサルティングの佐藤です。(‘◇’)ゞ
購入材料の入数を合わせよう...と、思ったことありませんか?
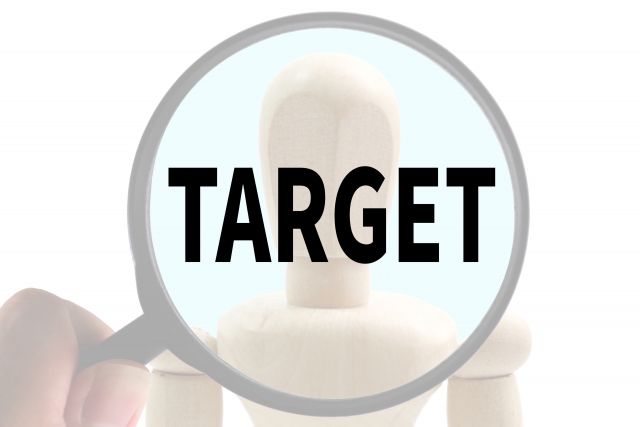
「それに何の意味があるの?」
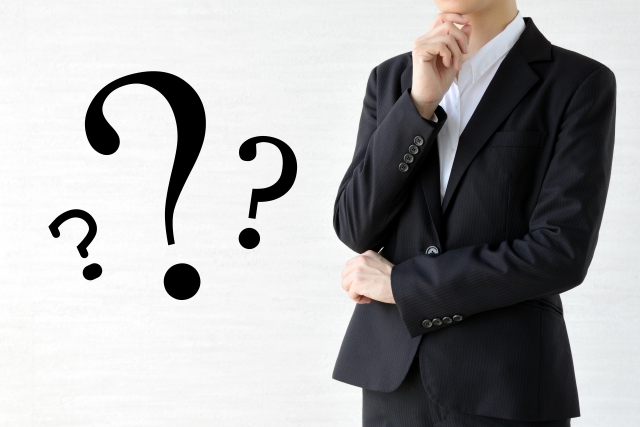
材料の入数を合わせると、改善になります。
「基板が500p/lotだから、部品も500p/lotにするの?」
それは違います。
各部品の使用数によって、考える必要があります。
例えば…
・基板 500p/lot
・搭載部品A 5p/1基板
・搭載部品B 8p/1基板
・搭載部品C 1p/1基板
こんな部品構成だとしましょう。
理想の材料入数は…
・基板 500p/lot
・搭載部品A 5p/1基板 ×500=2,500p/lot(+αは不良見込み分)
・搭載部品B 8p/1基板 ×500=4,000p/lot(+αは不良見込み分)
・搭載部品C 1p/1基板 ×500=500p/lot(+αは不良見込み分)
つまり、基板500pに対して、使用する材料が使いきれる入数です。
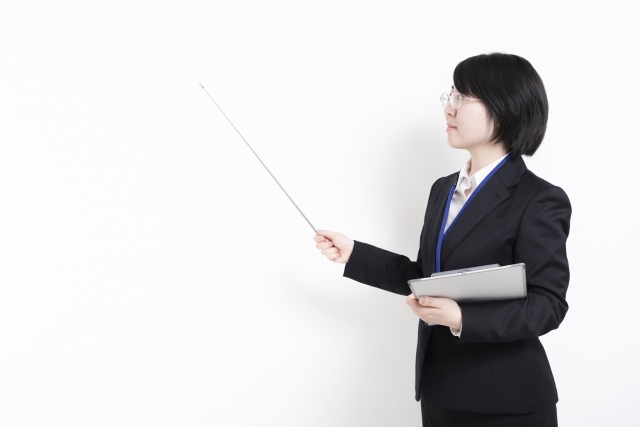
「それの何が改善になるの?」
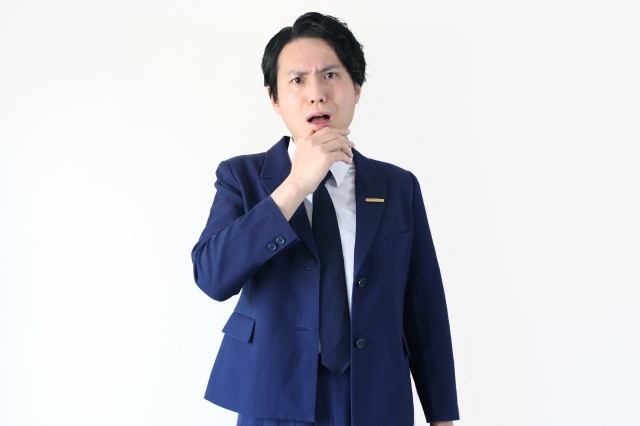
発注、入庫、仕掛、在庫の管理工数が、一括してできる。
もし、バラバラなら、サイクルが合わずに、その都度実施することになります。
同時にできれば、工数は減るはずです。
無駄も取れますし、その方が、合理的だと思いませんか?
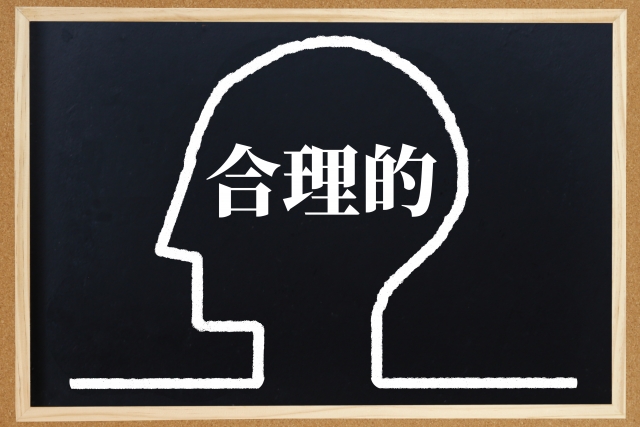
できる、できないは別にして、「こうなったら工数削減できるよね?」ということ、他にもありませんか?
改善の発想は、固定概念を無視して、理想を追求してみましょう。
発想しない限り、改善に向けての行動は起こせません。
「改善はやってるけど、最近停滞しているな」
そう感じることがあるならば、改善の発想が、枯渇しているかもしれません。
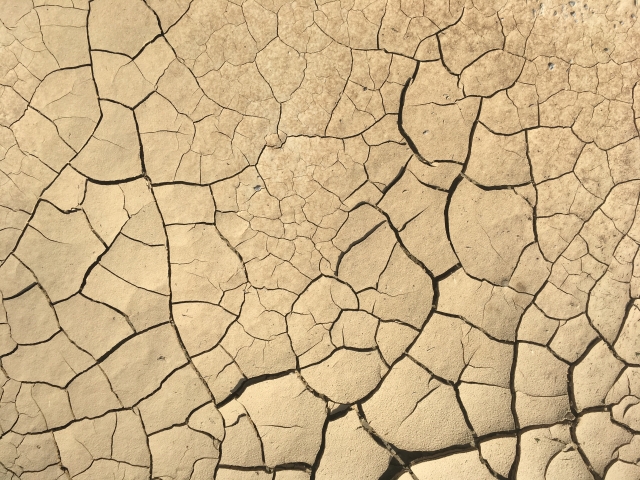
こんな課題を解決したい…、ぜひ、ご相談下さい。
儲かる仕組みづくりの、お手伝いをさせて頂きます。
See you tomorrow ♬
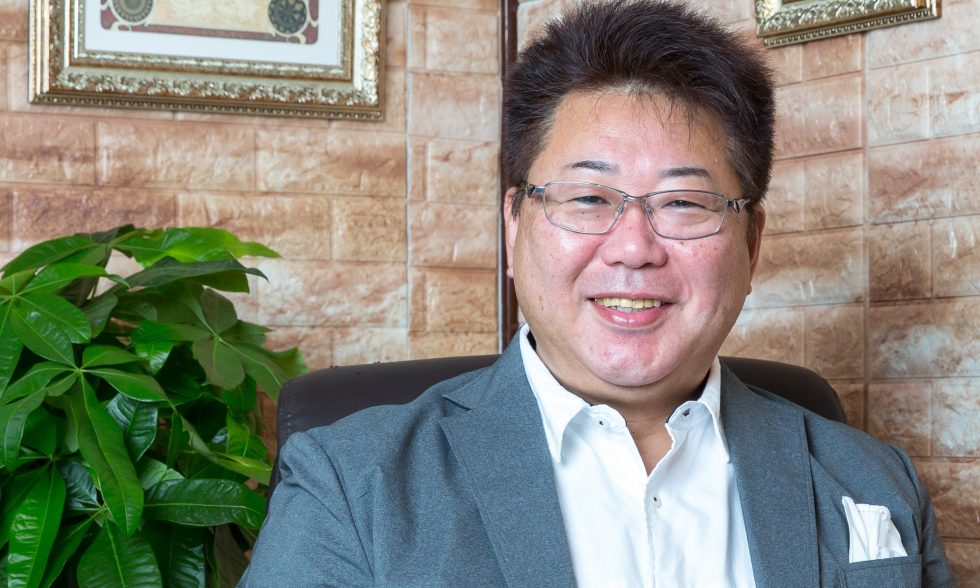
ディーズビジネスコンサルティング 佐藤
お問い合わせは、下記ホームページのお問い合わせをクリック。
※モバイルの場合は、ブログの✉相談してみるを、クリックしてもOK。
必要事項を、ご記入ください。
内容を確認させて頂き、返信させて頂きます。
お問合せを頂いたとしても、こちらから、一方的な営業メール、電話、訪問は致しません。
お気軽に、お問合せを。