慢性不良と突発不良…工程内不良の改善は、二つを切り分けて取り組みましょう
品質
2022.02.04
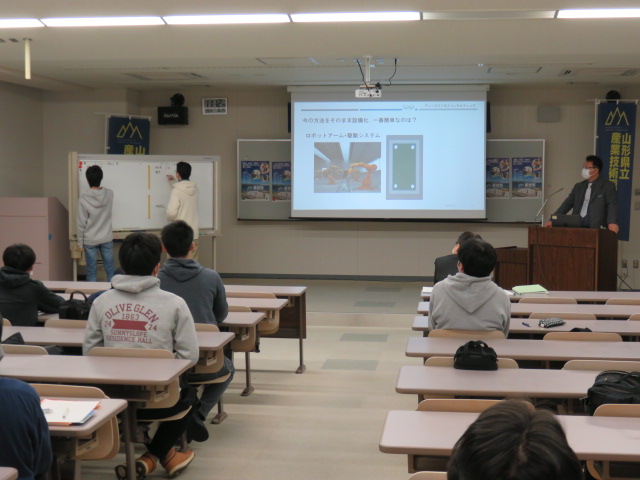
地域活性化の為に魅力ある地方企業づくりのお手伝いをさせて頂く、
ディーズビジネスコンサルティングの佐藤です。(‘◇’)ゞ
工程内不良、頭の痛い問題ですよね。
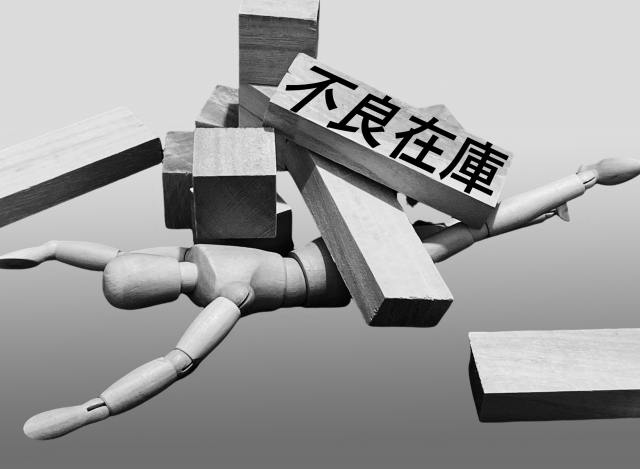
作ったものが不良になる。
お金も時間も、全てマイナスへ。
当然、利益もマイナス。
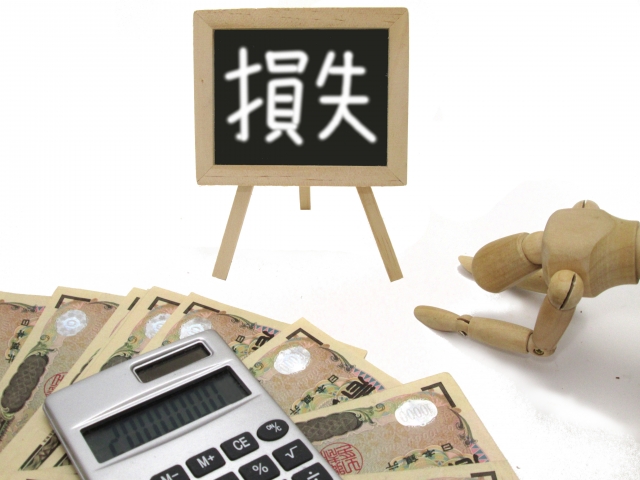
ものづくりにおいて、無くしたい無駄の一つが、工程内不良です。
よって、当然、改善に取り組んでいるはず。
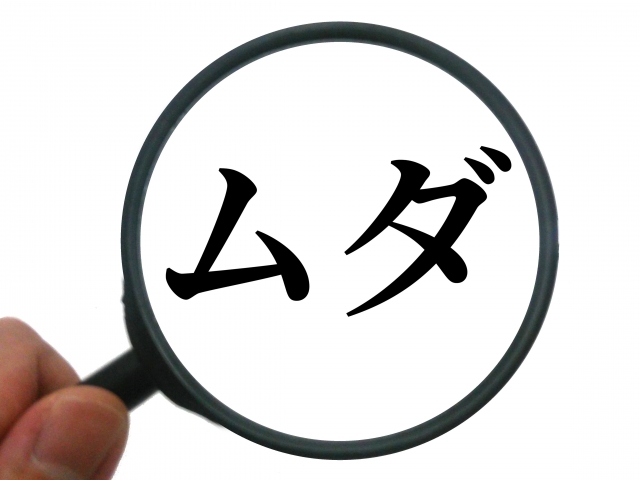
工程内不良には、大別すると二つあります。
一つは慢性不良、日々一定数現れる不良。
もう一つが突発不良、ある日突然発生する不良。
ゲリラ豪雨のようなものですね。
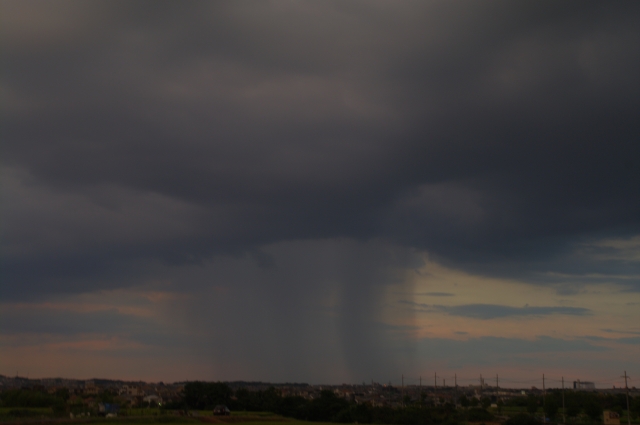
同じ不良ですが、改善のアプローチに違いがあります。
今日は突発不良のアプローチについて、記載していきます。
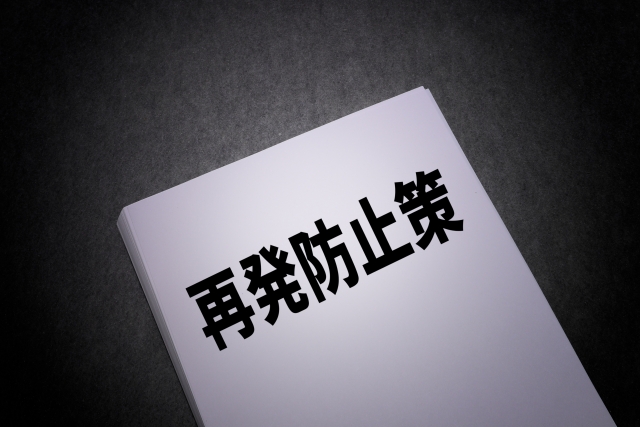
突発不良の場合、まず考えるべきこと。
それは、「なぜ、気付かずに不良が作られたのか?」です。
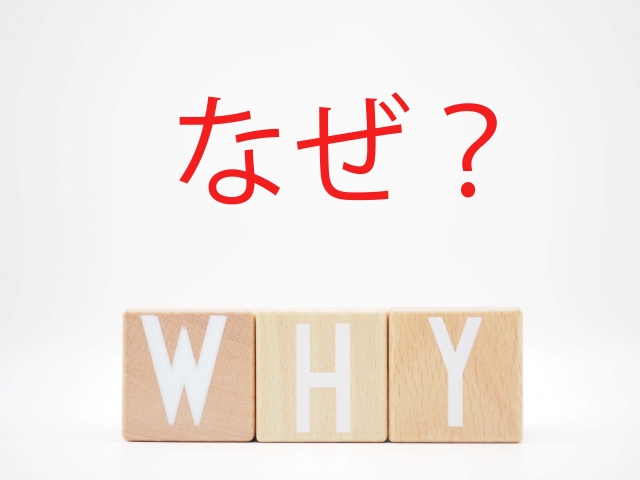
全く想定外の事象なのか?
それとも予測の範疇か?
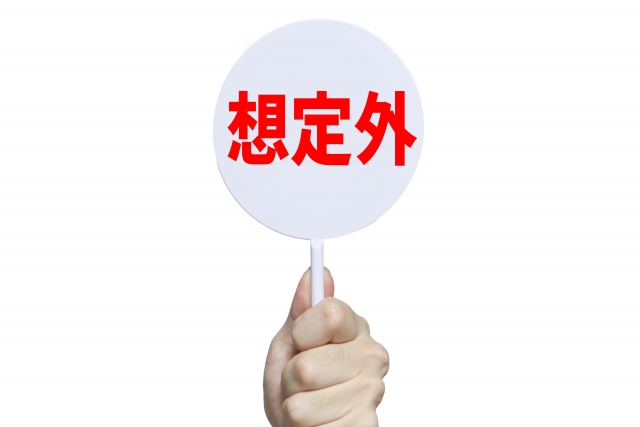
想定外の場合、何が足りなかったのか?(FMEA等のQCツールの不備?)
予測範疇の場合、どこに抜け漏れがあったのか?(4M)
突発不良を出さない為には、連続で不良が作られない工程を構築しましょう。
発生よりは、流出重視。
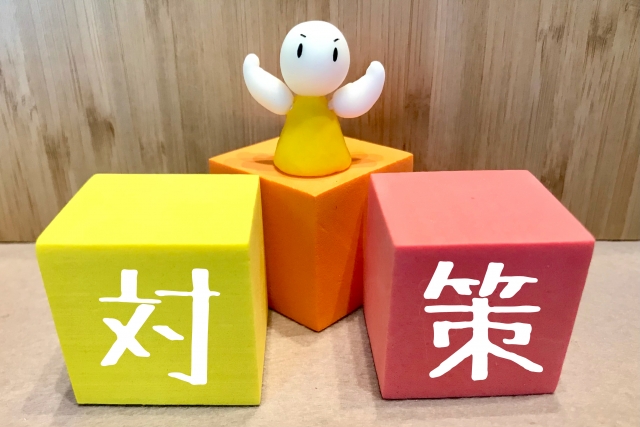
理想は発生源を特定し、手を打つですが、流出を先に潰しましょう。
どうすれば、生産中に気付けるか?
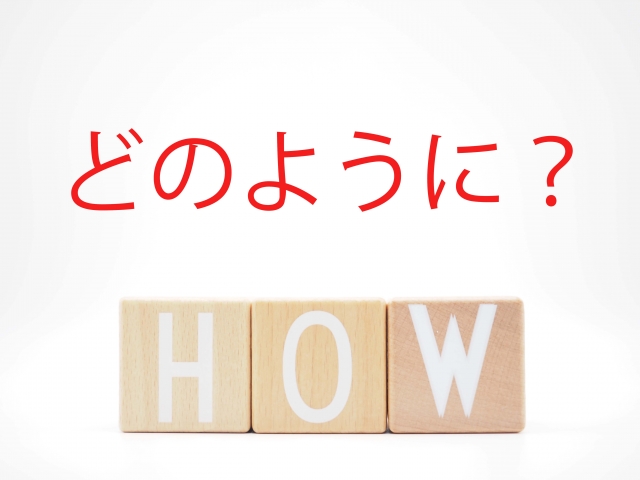
次に、当該事象から、類似事象を推察し、気付く仕掛けを作り上げる。
それから、発生源が効果的です。
とにかく、連続して作らないをポイントに。
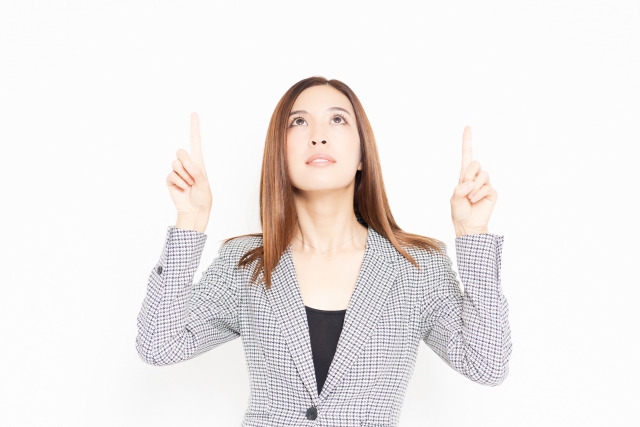
突発不良でロットアウト→一日の生産品が廃棄対象になれば、大きなロス。
作り直しも、しなければなりません。
突発不良→まず気付いて止める...を優先に取り組みましょう。
慢性不良は、また別の機会に…。
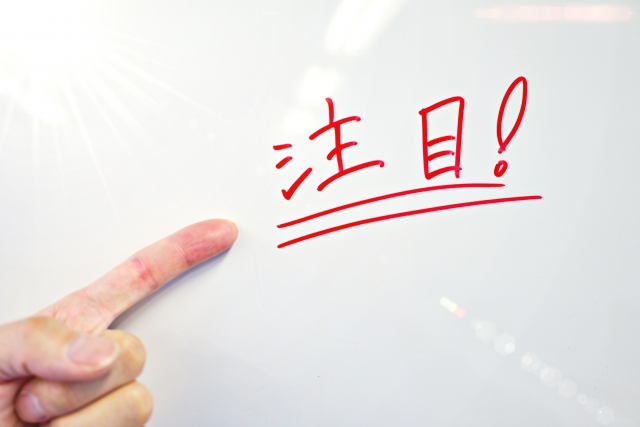
こんな課題を解決したい…、ぜひ、ご相談下さい。
儲かる仕組みづくりの、お手伝いをさせて頂きます。
See you tomorrow ♬
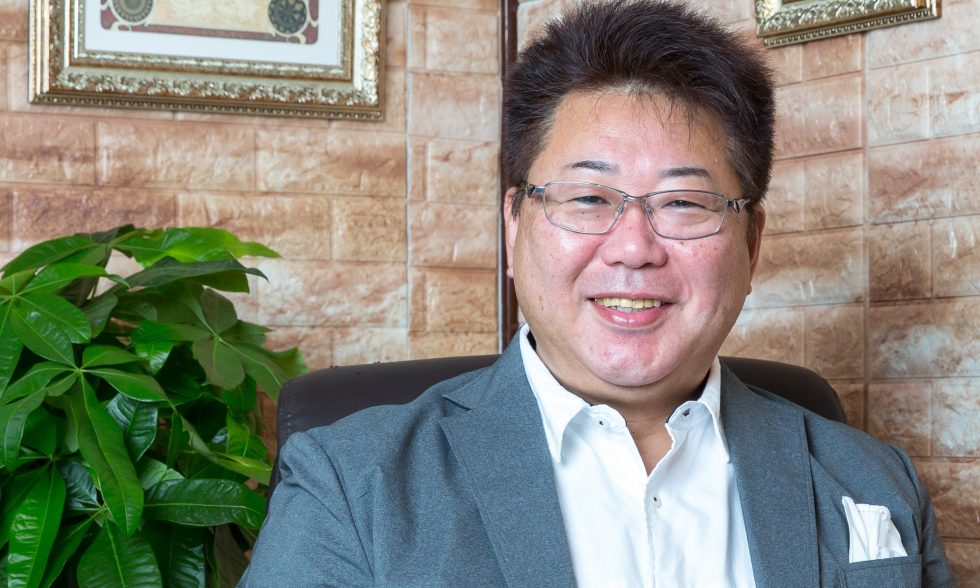
ディーズビジネスコンサルティング 佐藤
お問い合わせは、下記ホームページのお問い合わせをクリック。
※モバイルの場合は、ブログの✉相談してみるを、クリックしてもOK。
必要事項を、ご記入ください。
内容を確認させて頂き、返信させて頂きます。
お問合せを頂いたとしても、こちらから、一方的な営業メール、電話、訪問は致しません。
お気軽に、お問合せを。