特性要因図…みんなで作る意味
品質
2023.03.14
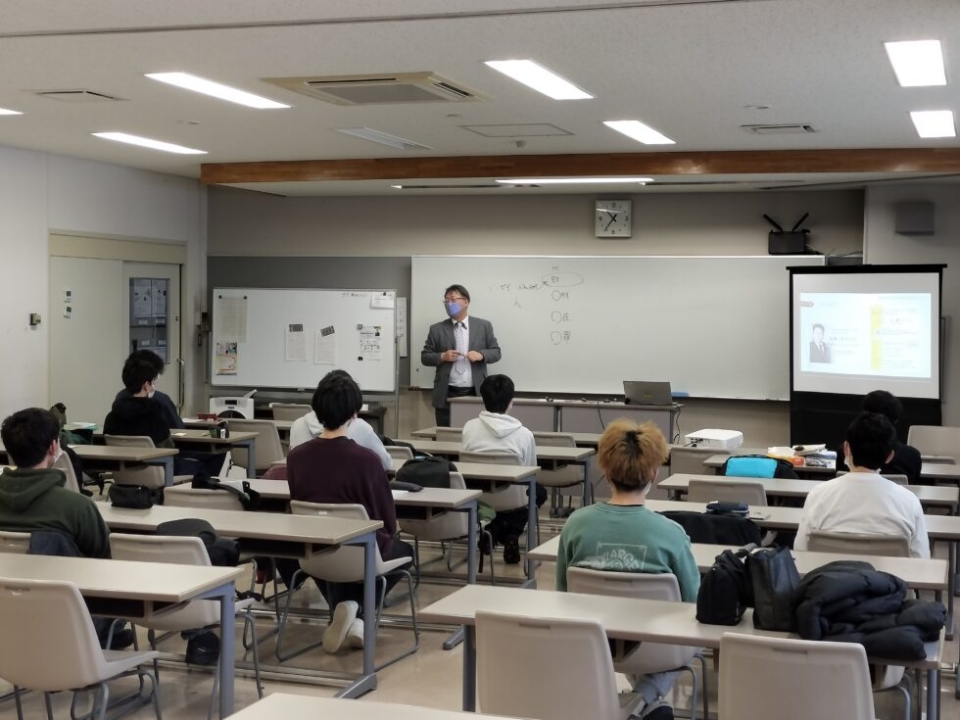
地域活性化の為に魅力ある地方企業づくりのお手伝いをさせて頂く、
ディーズビジネスコンサルティングの佐藤です。(‘◇’)ゞ
特性要因図って、どうやって作っていますか?

「それは品質管理部署で作っているよ」
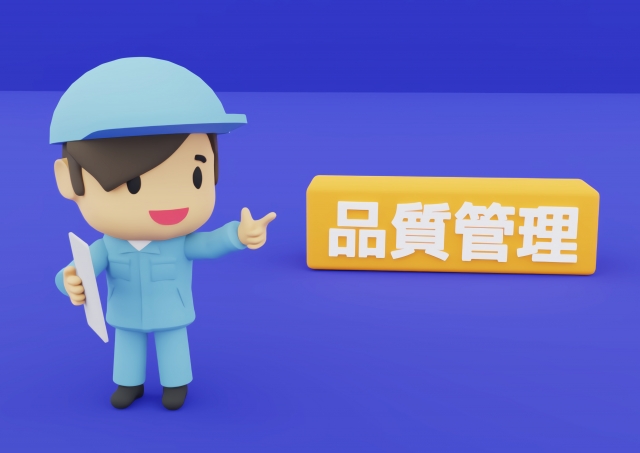
仕上げは品質管理部署でしょう。
では、作る時にどんなメンバー集めていますか?
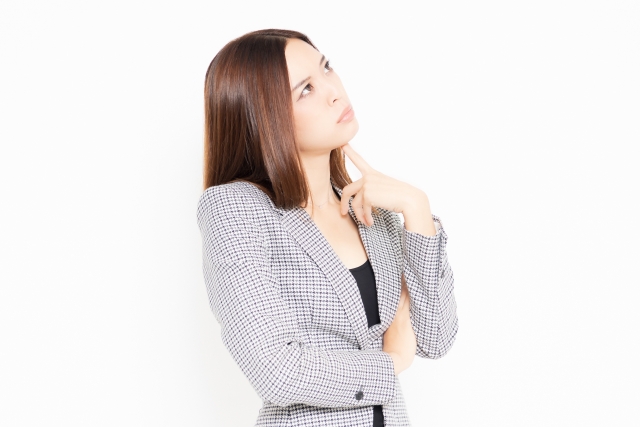
特性要因図は品質管理ツール。
品質記録に指定している会社もあるでしょう。
その為、品質管理部署が作成するもの…となりがち。
仕上げという部分では間違いではありませんが、それでは不十分な特性要因図になっているかも知れません。
不十分になる理由は、「情報不足」です。
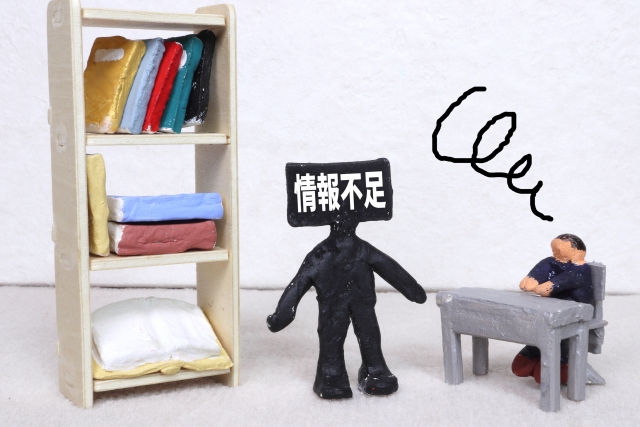
特性要因図の要因を大類すると「材料、人、設備、方法→4M」ですよね。
4Mごとに、考えられる要因、可能性を書き出していく。
品質管理部署は、4M総括している部署とも言えますが、メインは方法の部分ですよね。
材料のメインは、購買部署。
人のメインは、製造部署。
設備のメインは、技術部署。
こんな感じでしょうか?
少なくても、この関連部署のメンバーを集めて、特性要因図を作り上げるべきでしょう。
できるだけ、実際に作業、検査、管理しているメンバーを集めて、協議する。
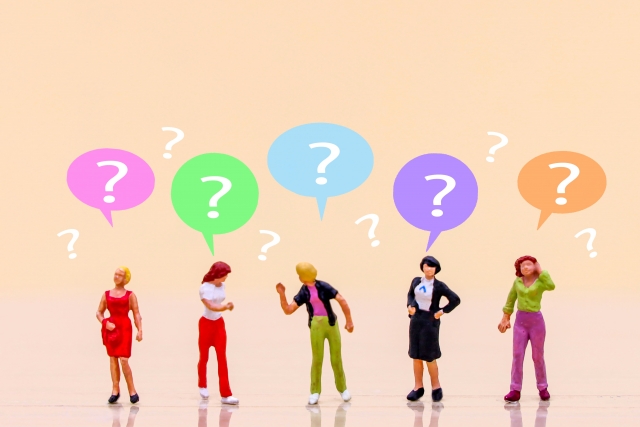
その上でポイントになる事。
※メイン担当部署の人に、他部署のメンバーが質問をしていく、疑問をぶつける
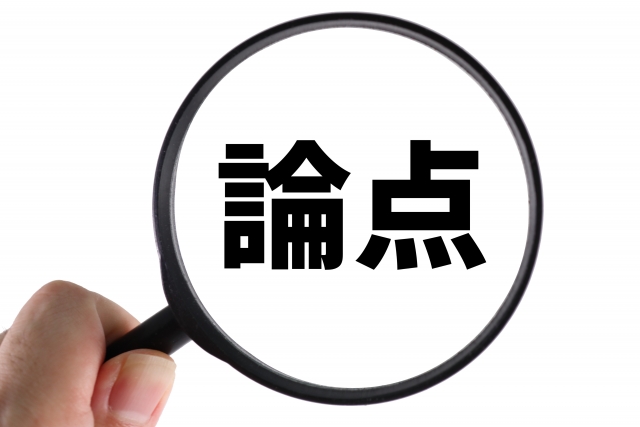
なぜか?
誰も自分の部署が対応しているところに、問題があると言い出しにくい。
どうしても、甘くなりがち。
形骸化した要因らしきものを書いてしまう。
自部署の防衛機能が働きやすいからです。
人ですから…しょうがない。
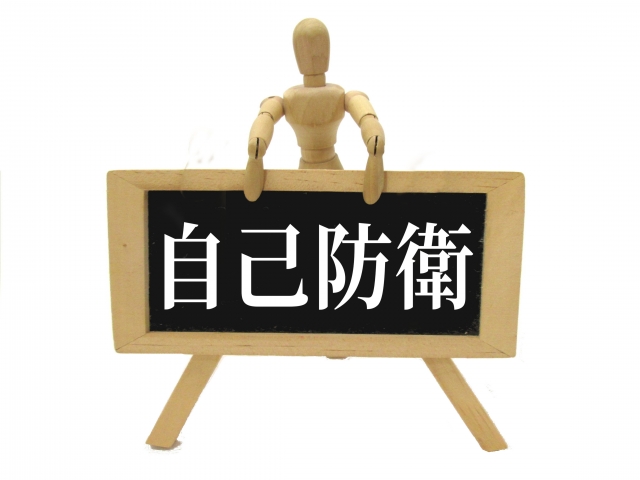
それを補うのが、他部署含めた横断的なメンバー。
異なる視点で、疑問を出せるから。
もっとも、なぁなぁのメンバーではNG。
ちゃんと言い合えるメンバーを集め、何でも言える環境を作るのが大切です。
その為には、どんな意見=異見も無視しない、否定しないを、共通のルールにしましょう。
今まで気付かなかったことに、気付ける為にも。
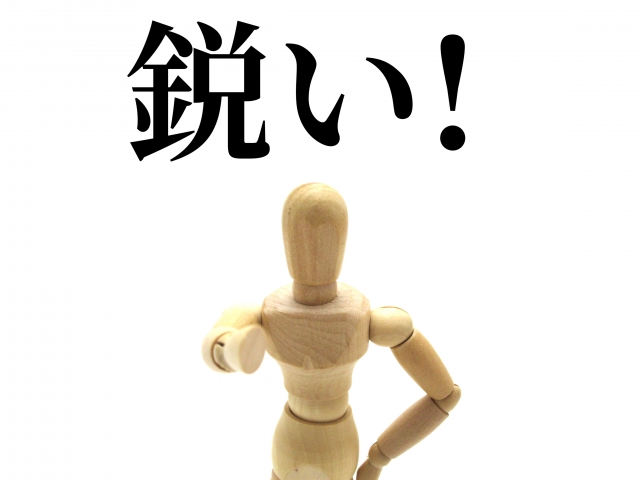
特性要因図の作成方法…様々な書籍にも書いてあるはずです。
でも、意外とできていなのかも知れません。
真の問題に辿り着かず、再発を繰り返しているなら…。
時間とお金を掛けても、本当の特性要因図を作るのは、長い目で見て価値があること。
あれば良い.、無いとまずい..で、形骸化した特性要因図など、無駄でしかありませんから。
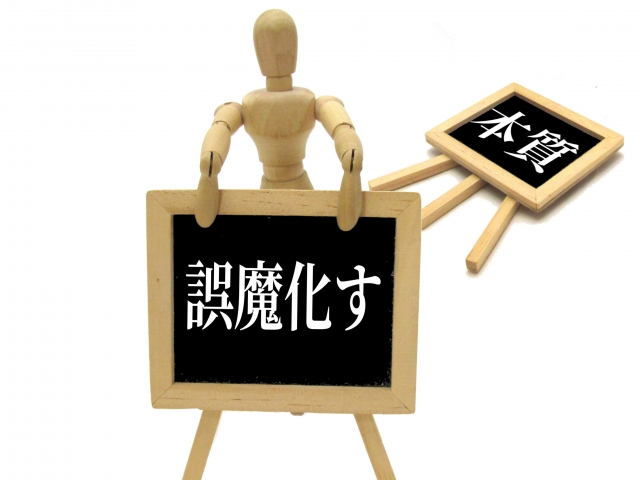
こんな課題を解決したい…、ぜひ、ご相談下さい。
儲かる仕組みづくりの、お手伝いをさせて頂きます。
See you tomorrow ♬
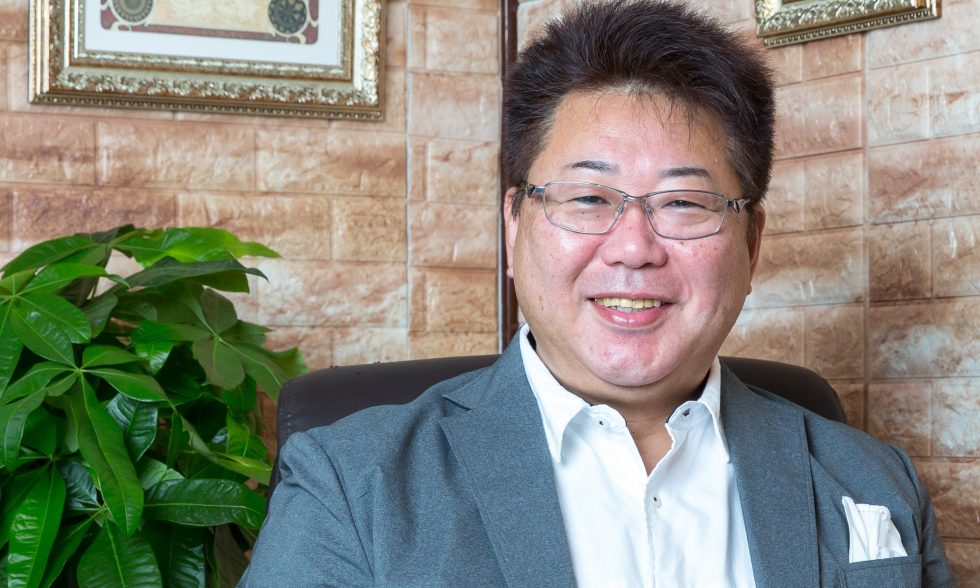
ディーズビジネスコンサルティング 佐藤
お問い合わせは、下記ホームページのお問い合わせをクリック。
※モバイルの場合は、ブログの✉相談してみるを、クリックしてもOK。
必要事項を、ご記入ください。
内容を確認させて頂き、返信させて頂きます。
お問合せを頂いたとしても、こちらから、一方的な営業メール、電話、訪問は致しません。
お気軽に、お問合せを。